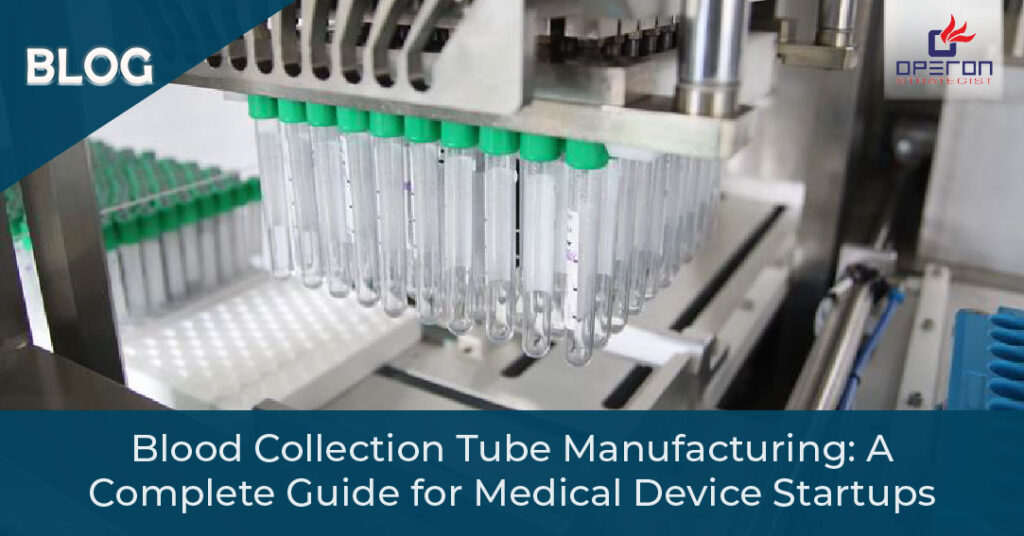
Introduction
The demand for diagnostic consumables, especially blood collection tubes, has surged due to increased healthcare awareness and diagnostic testing. For medical device startups and entrepreneurs in the USA, blood collection tube manufacturing presents a lucrative opportunity. But entering this market requires a deep understanding of the regulatory landscape, manufacturing process, and quality standards.
What Are Blood Collection Tubes?
Blood collection tubes are sterile, evacuated tubes used to collect and preserve blood samples for diagnostic testing. These tubes are made of plastic or glass and may contain additives like anticoagulants or clot activators, depending on their intended use.
Common Types of Blood Collection Tubes
- EDTA Tubes – For hematology testing
- Citrate Tubes – For coagulation tests
- Heparin Tubes – For plasma separation
- Serum Tubes – With or without gel separators
- Fluoride Tubes – For glucose testing
Each tube has specific color-coded caps based on the additive and intended application.
Market Potential for Blood Collection Tube Manufacturing
The global blood collection market is expected to surpass $10 billion by 2030, with a significant share from the USA. Factors fueling this growth include:
- Rising demand for diagnostic testing
- Government initiatives for disease prevention
- Increasing awareness about regular health screening
- Surge in chronic diseases and aging population
By establishing a compliant and quality-driven manufacturing setup, you can tap into both domestic and international markets.
Steps to Start Blood Collection Tube Manufacturing in the USA
- Market Research & Feasibility Study
- Analyze the demand and supply gap
- Identify competitors and pricing trends
- Evaluate distribution channels
- Forecast ROI and breakeven
- Choose the Right Manufacturing Facility Layout: A clean, contamination-free, and well-segregated layout is essential. Consider:
- ISO Class 7 or 8 cleanroom
- Automated molding and sealing machines
- In-line quality control and packaging units
- Design and Development Documentation
- Create comprehensive Design History Files (DHF) and Device Master Records (DMR) in line with FDA 21 CFR 820.30 for design control compliance.
- Regulatory Approvals and Classification: In the USA, blood collection tubes are classified as Class II medical devices. You must:
- Register your facility with the FDA
- Submit a 510(k) premarket notification
- Implement a compliant Quality Management System (QMS) as per 21 CFR Part 820
- Ensure proper UDI (Unique Device Identifier) labeling
Need help with FDA 510(k) submission or QMS implementation? Talk to our regulatory experts →
Raw Materials and Equipment Used
Raw Materials:
- PET/Glass Tubes
- Rubber Stoppers
- Additives (EDTA, Heparin, Fluoride, etc.)
- Plastic Caps and Color-coded Closures
- Labels and Packaging Material
Equipment:
- Injection Molding Machines
- Vacuum Filling Machines
- Additive Dispensers
- Labeling and Sealing Machines
- Cleanroom Equipment
Quality Control and Sterilization
Maintaining quality and sterility is non-negotiable in blood collection tube manufacturing. Ensure:
- Biocompatibility testing (ISO 10993)
- Endotoxin and sterility testing
- Leak and vacuum retention testing
- Accelerated aging and shelf-life studies
Sterilization methods: ETO (Ethylene Oxide) or Gamma Radiation
Key Compliance and Certification Requirements
To manufacture and sell in the USA, ensure compliance with:
- FDA 21 CFR Part 820 (QSR)
- ISO 13485:2016 Certification
- FDA 510(k) Clearance
- Labeling Requirements (21 CFR 801)
- UDI Compliance
Key Considerations for Success in Blood Collection Tube Manufacturing
Launching a successful blood collection tube manufacturing business requires strategic planning and awareness of industry expectations. Here are a few important considerations that, when addressed early, can ensure smoother operations and faster market entry:
- Initial Investment Planning: Setting up a compliant facility with cleanroom environments and automated equipment is essential. Proper budgeting and phased investment planning can help manage capital efficiently.
- Regulatory Preparedness: Understanding and fulfilling FDA and ISO 13485 requirements is critical. With the right guidance, regulatory approvals like 510(k) can be obtained without unnecessary delays.
- Documentation and Traceability: Implementing strong systems for batch tracking, labeling, and quality documentation ensures long-term compliance and builds trust with buyers.
- Product Quality and Consistency: Investing in robust quality control systems and validation processes ensures your products meet international standards and customer expectations.
With expert consulting and turnkey support, these considerations become opportunities to build a strong foundation for long-term success.
Why Partner with Operon Strategist?
At Operon Strategist, we help medical device startups and manufacturers in the USA:
- Set up FDA-compliant manufacturing facilities
- Prepare design & development documentation
- Obtain FDA 510(k), ISO 13485, and CE Mark certifications
- Train staff on QMS and regulatory compliance as per 21 CFR part 820
- Manage post-market surveillance and audits
We specialize in turnkey project consulting—from concept to commercialization.